1st Year, Stamps School of Art & Design
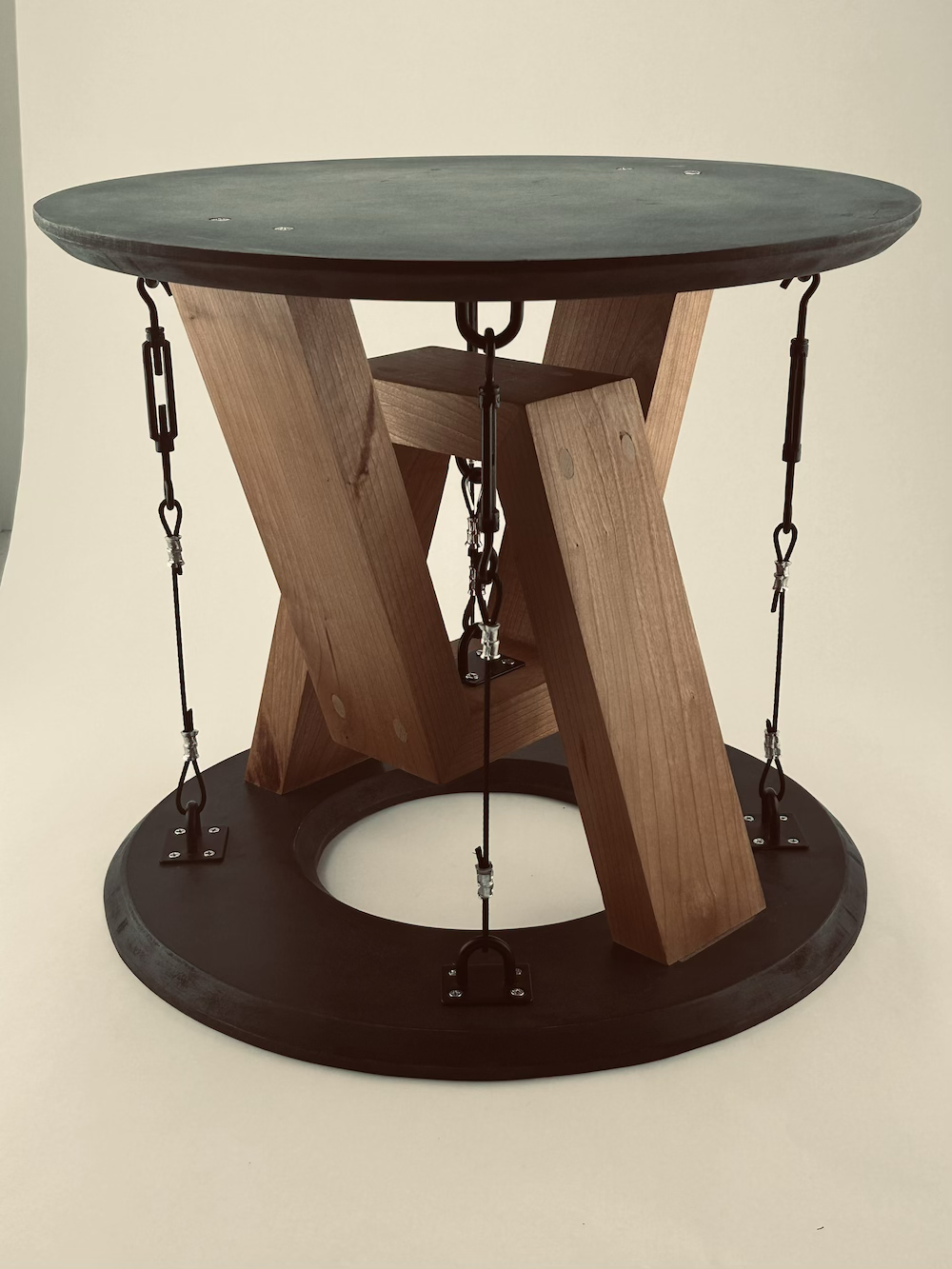
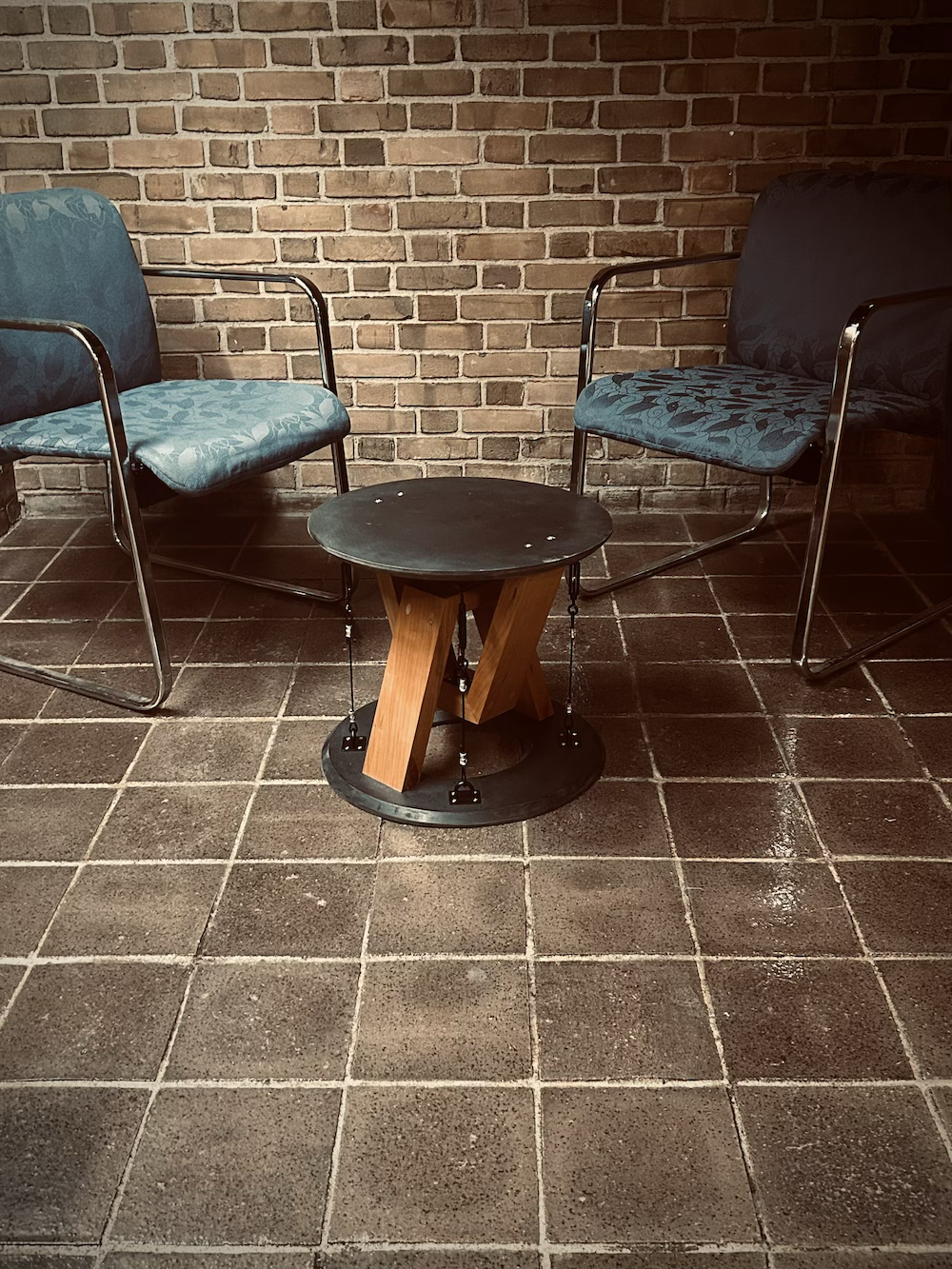
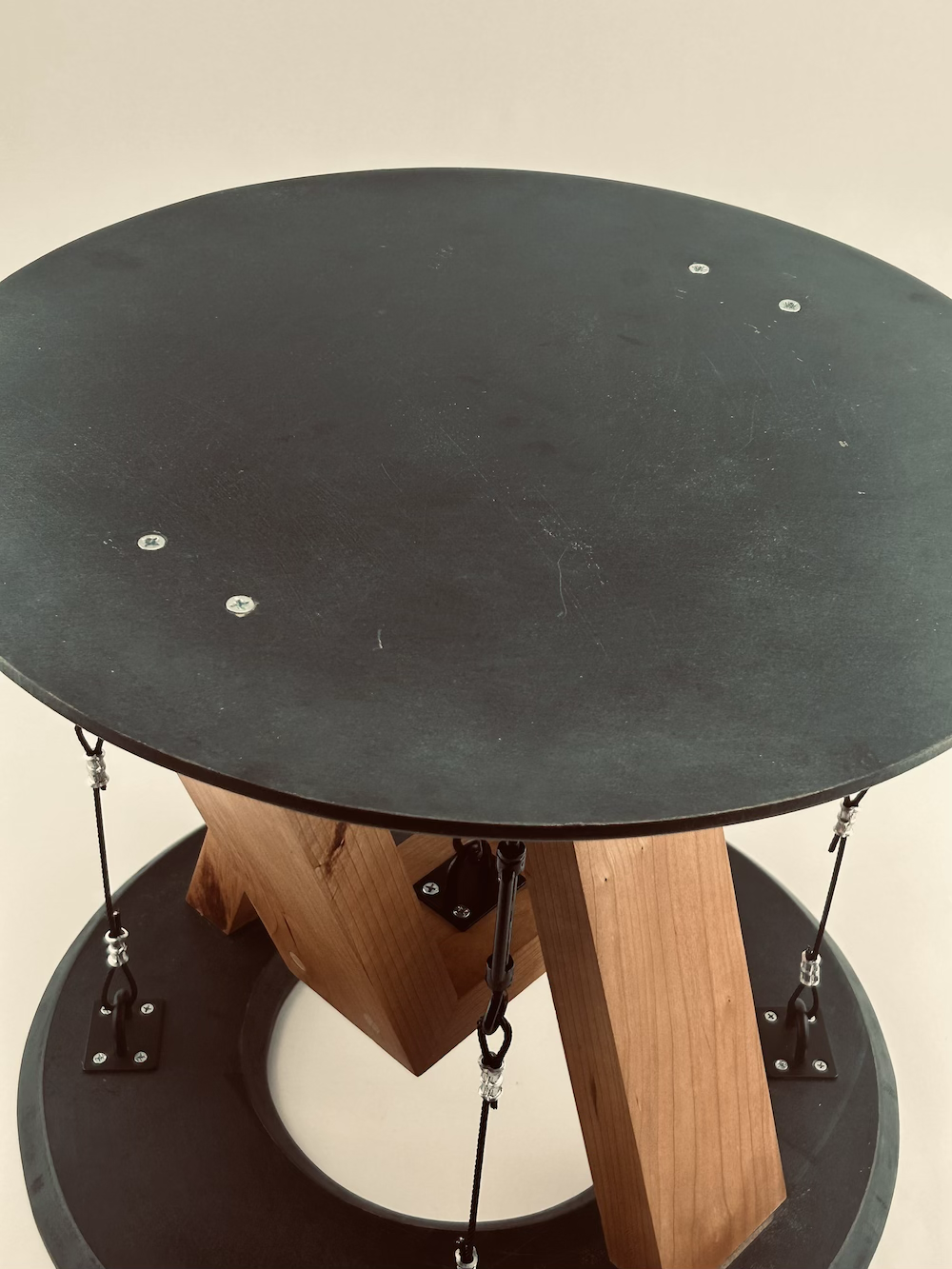
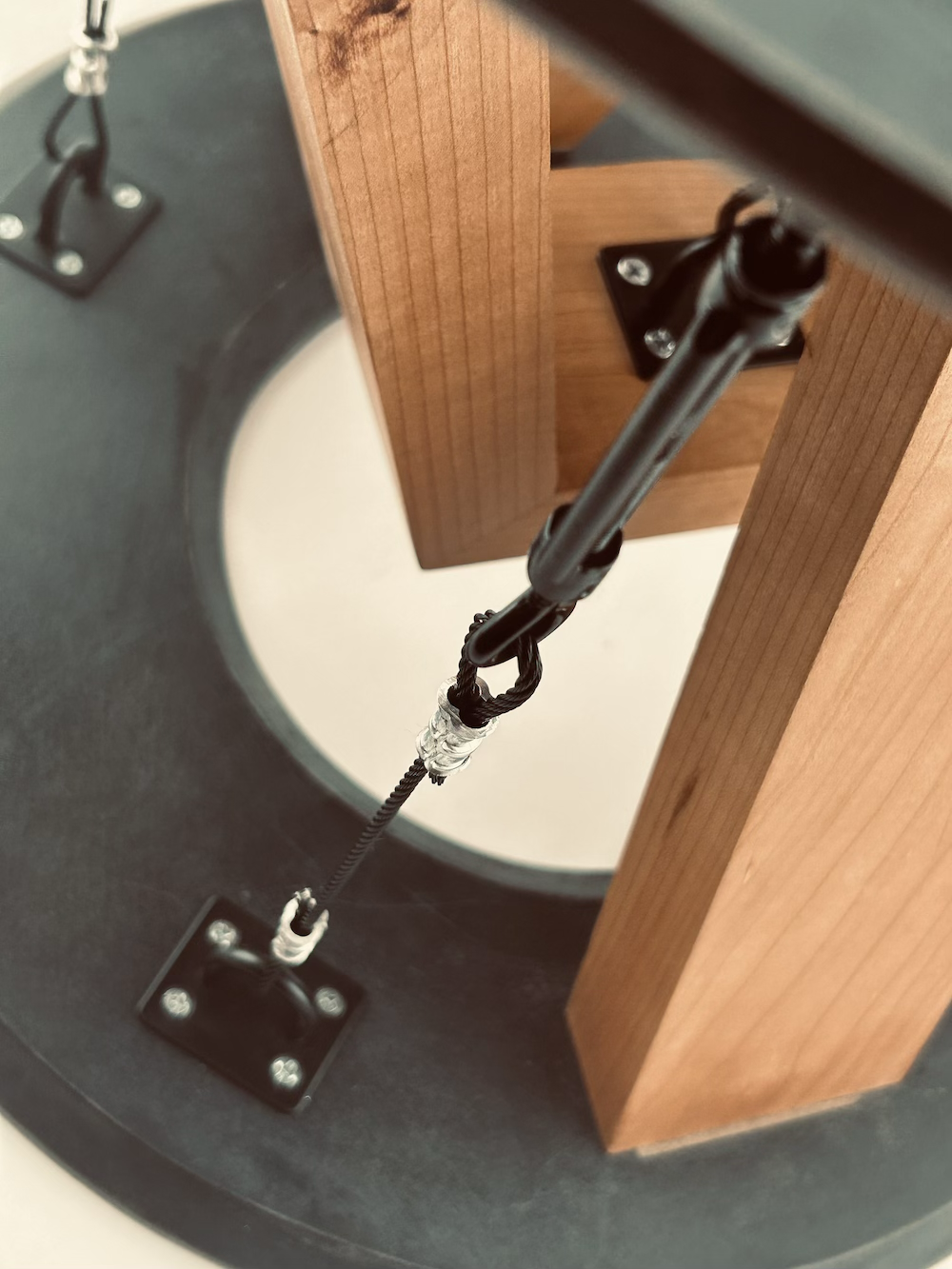

Wood working, Metal working, Sculpture
Abstract
The floating stool seamlessly blends science and artistry, leveraging the tensegrity principle for its striking, gravity-defying design. Developed from fifteen initial concepts, the final design was perfected through 3D modeling and crafted from cherry wood and MDF in a meticulous 36-hour process. Aircraft cables with high tensile strength ensure stability, while precise measurements and custom jigs facilitate accurate assembly. The stool’s base and top were painted charcoal gray and polished for a refined finish, while its legs were stained with beeswax. This innovative creation highlights the interplay of engineering, problem-solving, and craftsmanship, resulting in a stable yet seemingly floating structure.
The fabrication process demanded extensive problem-solving and the application of engineering principles. Custom modifications were made to clamps to support the irregular angles during glue-up, and specialized jigs were built to drill holes at precise angles. The stool’s seemingly magical, floating appearance is the result of a scientific principle called tensegrity. According to Oxford Languages, tensegrity is “the characteristic property of a stable three-dimensional structure consisting of members under tension that are contiguous and members under compression that are not.” This principle ensures that the structure remains stable and supported at all times, regardless of the force applied.
To enable the stool to bear the weight of a human, aircraft cables with a tensile strength exceeding 1,400 pounds were employed. These cables were carefully measured, cut to exact lengths, crimped, and tensioned to precise specifications, ensuring the tensegrity principle was fully realized. The woodwork began with a large rectangular block of cherry wood, which was cut and planed into boards for assembly. The stool’s base and top originated from a square sheet of MDF, which was expertly cut into perfect circles and beveled to harmonize with the legs of the stool. These components were then painted charcoal gray and polished using a combination of techniques while the paint was still slightly wet, creating a unique finish.
The legs of the stool were sanded to a smooth finish using 220-grit sandpaper and treated with all-natural beeswax for a rich, lustrous appearance. Precision tools such as compasses, rulers, and squares were utilized to ensure the accurate placement of hardware. Even the slightest misalignment could compromise the stability and cause the tensegrity forces to fail, underscoring the meticulous care involved in this process.